Extension Springs
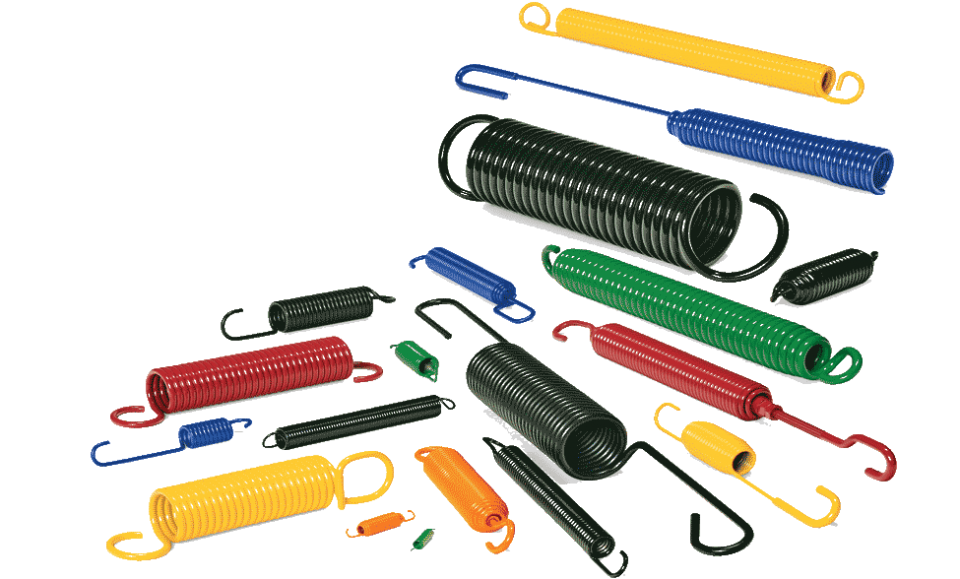
Extension Springs
Offer resistance to pulling forces and can be designed with varying amounts of resistance. WCS can design and produce this type of spring in the following variations.
- .008 to .625” (.2 to 16 mm) Wire Diameter
- Adjustable Initial Tensions
- Variable hook types
- Able to provide completely custom designs
- Able to apply multiple types of corrosion protection
- Stock inserted hook designs that allow quick flexibility
- Multiple Material Types and shapes
Initial Tension
Most extension springs are wound with initial tension.This is an internal force that holds the coils tightly together. The measure of the initial tension is the load necessary to overcome the internal force and just start coil separation. Unlike a compression spring, which has zero load at zero deflection, an extension spring can have a preload at zero deflection.
Note that there is a range of stress (and, therefore, force) for any spring index that can be held without problems. If the designer needs an extension spring with no initial tension, the spring should be designed with space between the coils
Have a question or need to order? to expedite the process
Machine Hooks
are the most common hook types used in most commercial spring applications. Inexpensive to manufacture and easily configured make this end type a popular choice. The last coils of the coil body in this type of design can be tapered to reduce hook stresses if needed.
Crossover Hooks
are the second most common hook in commercial applications and can offer longer fatigue lives due to their smaller breakover radii. The last coils of the coil body in this type of design can be tapered to reduce hook stresses if needed.
Extended Hooks
are used anytime the length of the hook must exceed the outside diameter of the last coil on the spring. The last coils of the coil body in this type of design can be tapered to reduce hook stresses if needed.
Inserted Hooks
have specific components that include a spring body, special hook of larger wire diameter and a cone that allows the hook to “swivel” inside of the coil body. WCS has developed an exhaustive list of standard hooks and cones to accommodate the usual tight timelines needed in developing a solution for a spring breaking in the field or if hook stresses prove to be too high during the design process.
Stresses in Extension Spring Ends
Often stresses are higher in the spring ends than in the spring body. Unless special design precautions are taken, the allowable body stress must be reduced. The hook stress in torsion should not exceed 40-45 percent of tensile strength, while hook stress in bending should not exceed 75 percent of tensile strength.
The maximum bending stress in a machine loop (see spring image below) occurs at location B, while the maximum torsion stress occurs at T. Stresses at these locations are estimated as follows: